Im Zuge eines netten Grillabends wurde beschlossen, dass ein sehr
netter Bekannter einen Oberhitzegrill benötigt und ich diesen bauen
sollte.
Die 3D Konstruktion war auf Basis einer fertigen
Konstruktion eines Forenkollegen schnell erstellt und im Gespräch mit
einigen
Arbeitskollegen bekam ich den "Auftrag" noch weitere 3 OHGs
zu bauen.
| 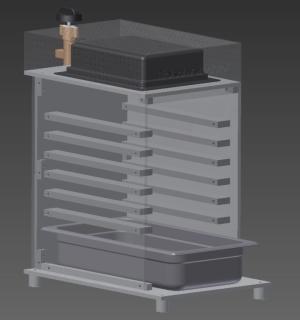 |
1. Wie immer wurde vorab eine 3D Konstruktion erstellt. Ein sehr netter Forenkollege hat ebenfalls einen Oberhitzegrill gebaut und seine Konstruktionszeichnungen zur Verfügung gestellt. Diese habe ich auf meine Anwendung hin abgeändert. Die Pläne werde ich im Downloadbereich meiner Seite ablegen. |
| 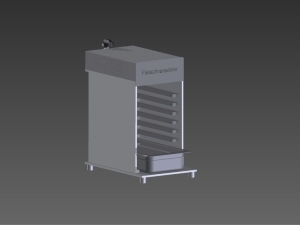 |
2. Die fertige Konstruktion aber noch ohne Grillrost. |
| 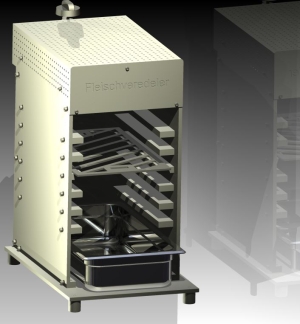 |
3. Der fertige Oberhitzegrill sollte so aussehen. |
| 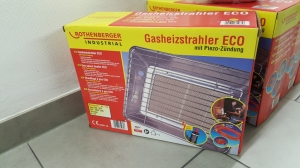 |
4. Als Wärmequelle wird ein handelsüblicher Heizstrahler verwendet. Es handelt sich um einen 4kW Strahler für die direkte Montage an einer Gasflasche. |
| 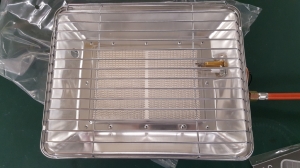 |
5. So kommt der Strahler aus der Verpackung. |
| 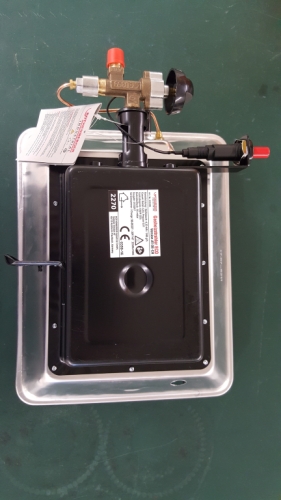 |
6. Hier kann man die Anordnung der Piezozündung gut sehen. Die Metallstreben wurden später abgeflext. |
| 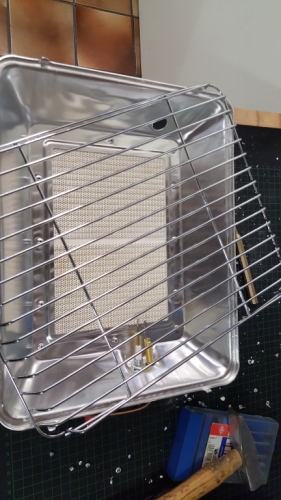 |
7. Alle überflüssigen Teile werden Stück für Stück demontiert.... |
| 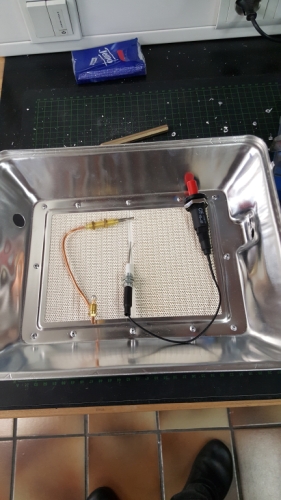 |
8. .... und teilweise verschrottet. Die Zündelemente werden natürlich später wieder benötigt. |
| 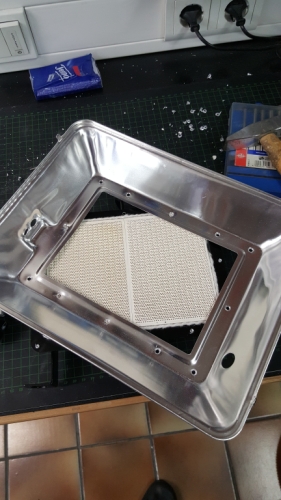 |
9. Die Verbindungsnieten wurden ausgebohrt und der Alurahmen entfernt. |
| 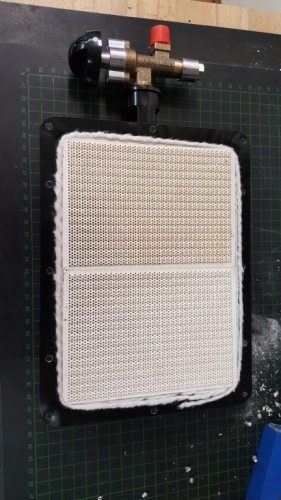 |
10. Der Brenner mit Gasregler und Dichtschnur. |
|  |
11. Nach ein paar Tagen wurden die bestellten Alu-Teile geliefert. Ich habe hier eine AlMg3 Legierung gewählt da diese lebensmittelecht ist. |
| 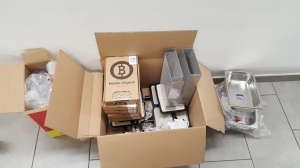 |
12. Hier liegen alle Kaufteile zusammen. Brenner, Grillroste vom Originalhersteller, Fettwannen und die benötigten Lochbleche. Diese habe ich direkt kanten lassen. Die Fettwannen sind GN 1/3 Wannen mit 65mm Höhe. |
| 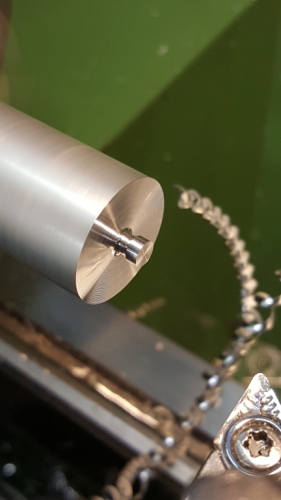 |
13. Aus dem 20mm Rundmaterial werden die Standfüsse für den OHG hergestellt. Hier wurde gerade der Zapfen für das M4 Befestigungsgewinde angedreht. |
| 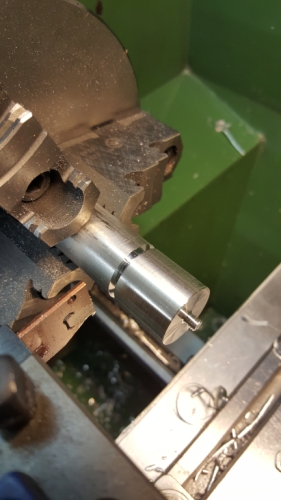 |
14. Das Überkopfabstechen im Linkslauf hat sich auf meiner keinen Drehbank als vorteilhaft erwiesen. |
| 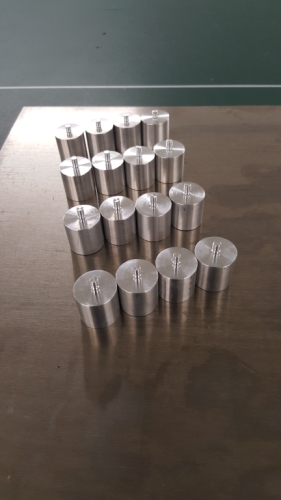 |
15. Die fertigen Standfüsse für 4 OHGs. |
| 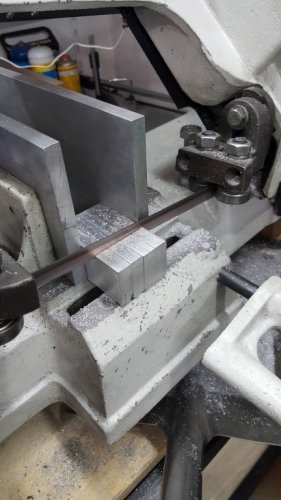 |
16. Nun wurden die benötigten Einzelteile zugesägt. |
| 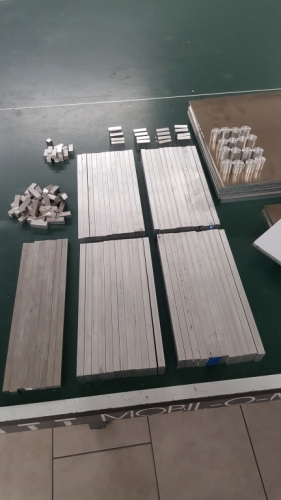 |
17. Bei 4 OHGs kommen schon viele Einzelteile zusammen. Da meine Werkbänke im Bastelkeller dafür zu klein waren musste die Tischtennisplatte im Nachbarkeller als Werkbank aushelfen :-) |
| 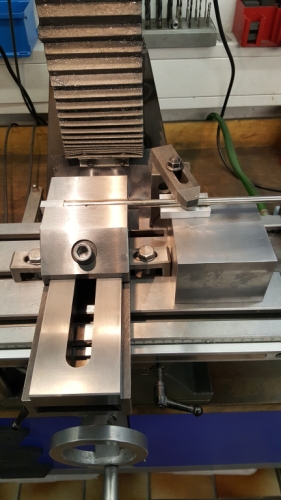 |
18. Bei einer Serienfertigung ist es immer einfacher sich Hilfsmittel zu bauen. Hier ist es ein einfacher Anschlag um nicht jedes Mal die Teile neu vermessen zu müssen. |
| 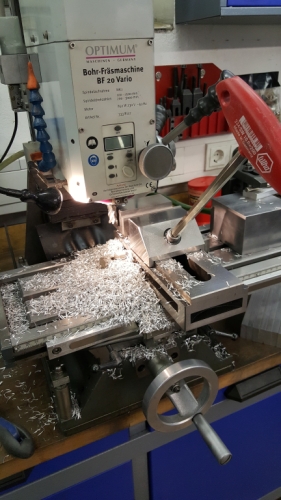 |
19. Nach und nach wurden alle Einzelteile auf Maß gefräst. Dabei kommen ganz schön viele Späne zusammen. |
| 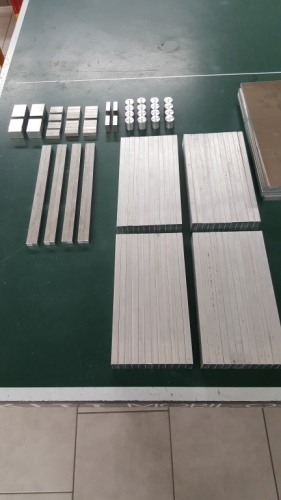 |
20. Alle Maße stimmen.... |
| 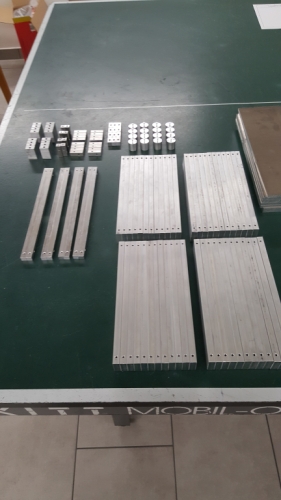 |
21. .... und es konnten anschließend die Löcher und Gewinde eingebracht werden. |
| 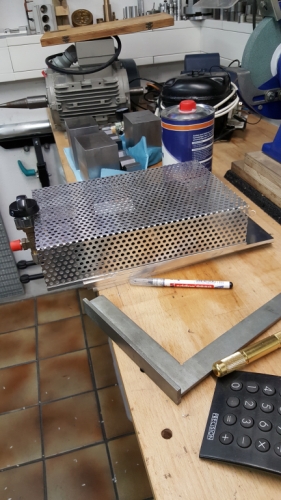 |
22. Hier wird der Sitz des Brenners unter der Lochblechverkleidung geprüft und auf der Brennerplatte angezeichnet. |
| 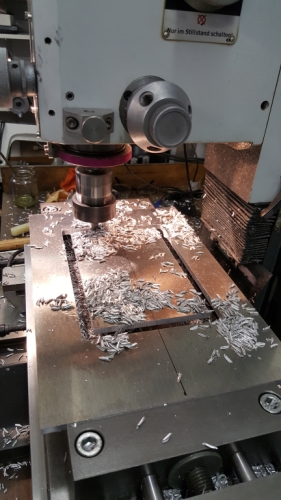 |
23. Der Ausschnitt für den Brenner wird gefräst... |
| 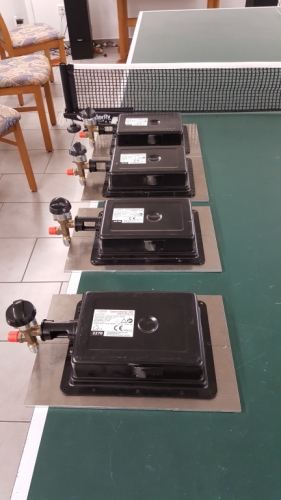 |
24. .... und der Sitz überprüft. Der Gasregler wurde um 90° gedreht. |
| 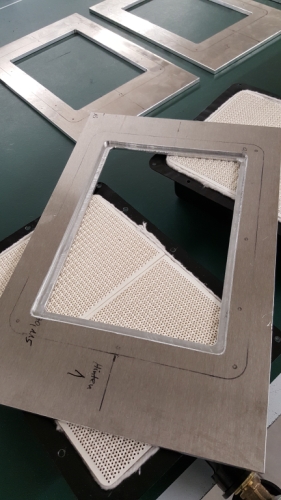 |
25. Zusätzlich zum Ausschnitt wurde eine umlaufende Nut eingefräst.Diese dient später zur Ausrichtung des Keramikteils. |
| 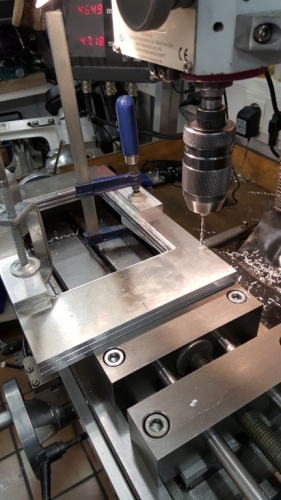 |
26. Alle Brennerplatten wurden in einer Aufspannung gebohrt. Vor Jahren habe ich mir glücklicherweise eine Aufspannvorrichtung für Bleche gebaut. Diese konnte ich nun sehr gut gebrauchen. |
| 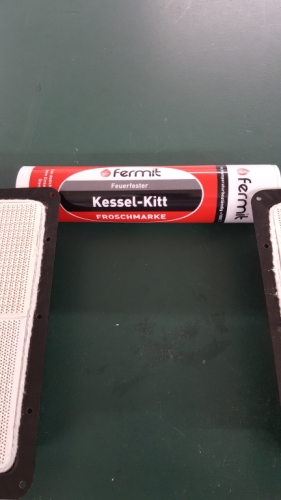 |
27. Da mir die Dichtschnur zur Brennerabdichtung nicht sicher genug war habe ich zusätzlich eine umlaufende Abdichtung mit Kesselkitt eingebracht. Das Material ist für Temperaturen bis 1000°C ausgelegt und dichtet zuverlässig. |
| 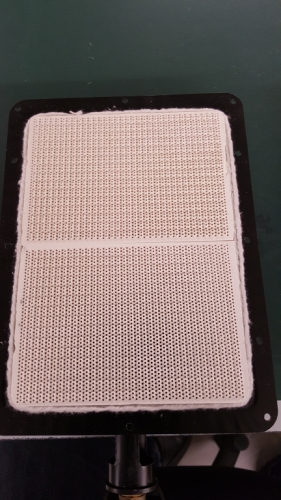 |
28. Der Brenner wird nun ... |
| 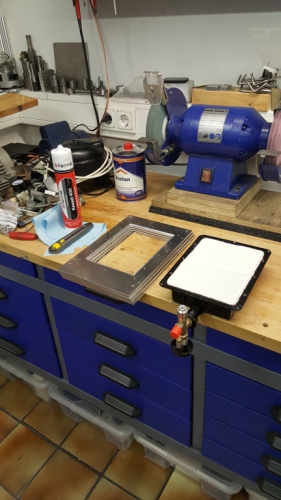 |
29. .... mit ausreichend viel Kesselkitt.... |
| 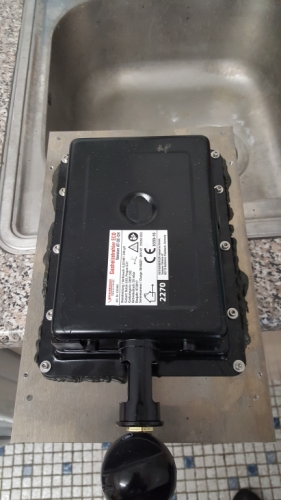 |
30. .... auf die Brennerplatte gesetzt und verschraubt. Der austretende Kitt kann einfach mit einem feuchten Tuch abgewischt werden. Hier möchte ich noch kurz anmerken, dass der Brenner mit 12 Schraubpunkten befestigt wurde. Es gibt auch günstigere Hersteller die aber nur 4...6 Befestigungspunkte vorsehen. Eine saubere Abdichtung gegen rückzündende Gase ist damit aus meiner Sicht nicht möglich. |
| 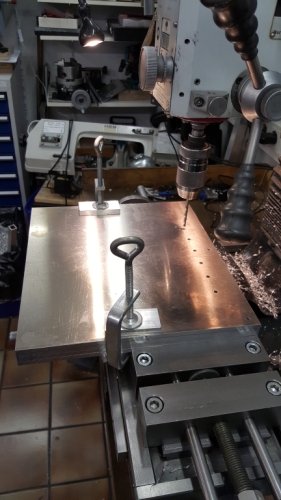 |
31. Nun ging es an die Seitenteile. Auch hierbei habe ich in einer Aufspannung alle Teile gebohrt. |
| 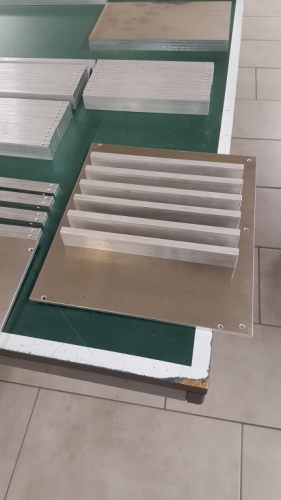 |
32. Die erste Montage der Einschubschienen. |
| 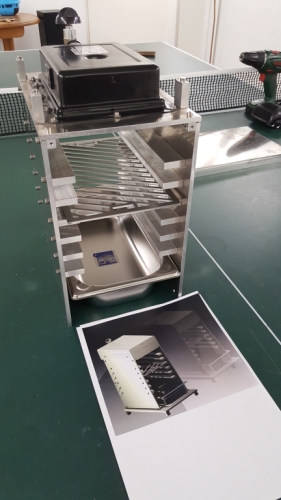 |
33. Konstruktion und Realität werden sich immer ähnlicher. |
| 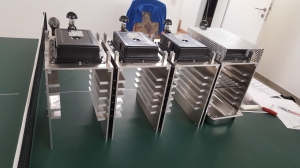 |
34. Stück für Stück werden die bearbeiteten Teile verbaut. |
| 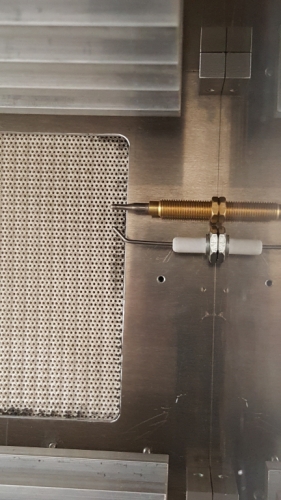 |
35. Die Rückwand der OHGs ist zusätzlich mit 2 Bohrungen ausgerüstet um die Piezozündung aufzunehmen. Diese sollte etwa 10mm unterhalb vom Keramikelement angebracht werden. |
| 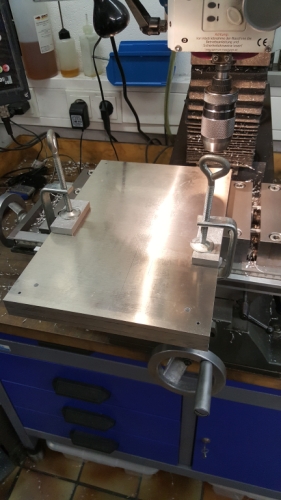 |
36. Nun wurden die Grundplatten bearbeitet .... |
| 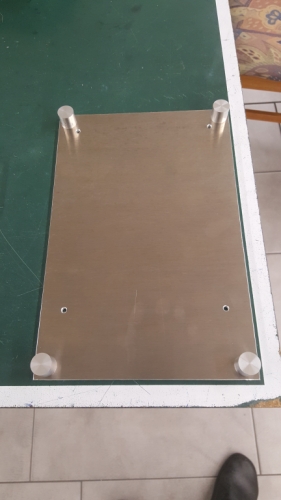 |
37. .... und die Standfüsse montiert. |
| 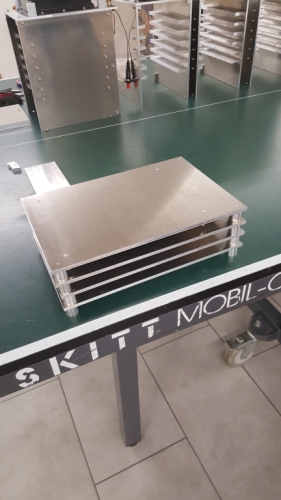 |
38. 4 OHGs und 4 Grundplatten. |
| 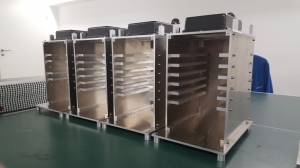 |
39. Sieht schon ganz gut aus. Es fehlen nur noch die Abdeckungen. |
| 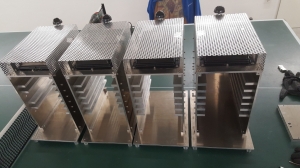 |
40. Nachdem die Lochbleche montiert waren.... |
| 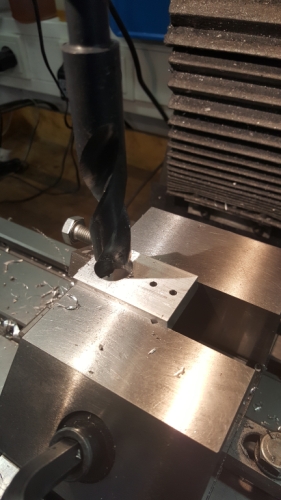 |
41. ....wurden noch schnell die Befestigungen für den Piezokünder hersgestellt. |
| 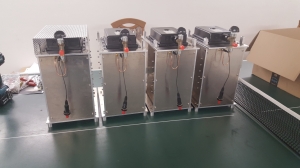 |
42. Die Rückseite der OHGs mit der vormontierten Zündung. |
| 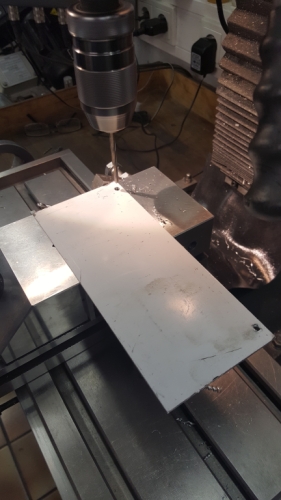 |
43. Die Frontblenden werden gebohrt .... |
| 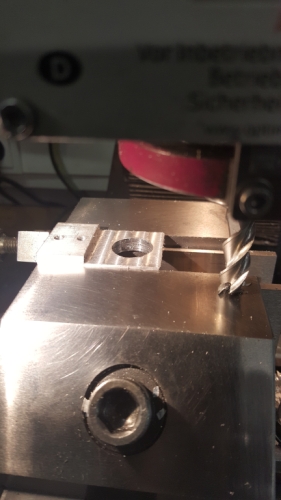 |
44. .... die Halter der Zündung angepasst.... |
| 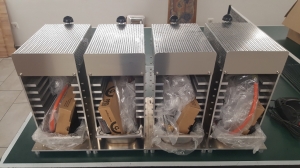 |
45. .... und alles montiert. Fertig sind die 4 Oberhitzegrills. Das Zubehör passt praktischer Weise direkt in den Grill. |
|  |
46. Die Rückseite mit fertig montierter Zündung. |
| 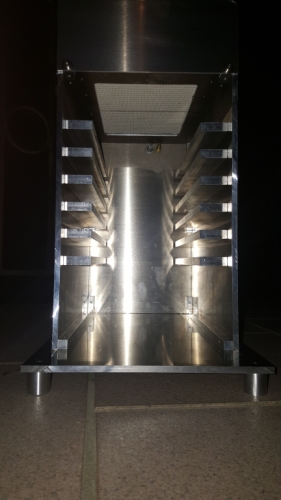 |
47. Nun ging es an den ersten Testlauf.... |
| 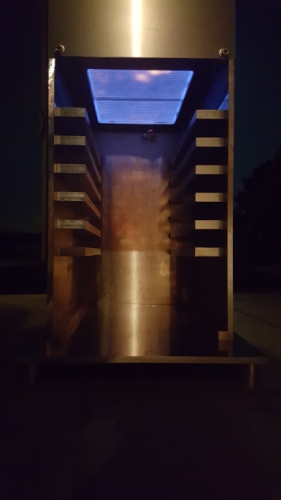 |
48. Der Brenner wurde gezündet und gibt ein schönes bläuliches Licht und viel Wärme von sich.... |
| 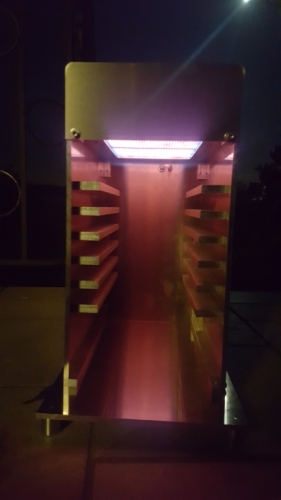 |
49. Nach ca. 7 Minuten strahlt alles in einem schönen Rot. |
| 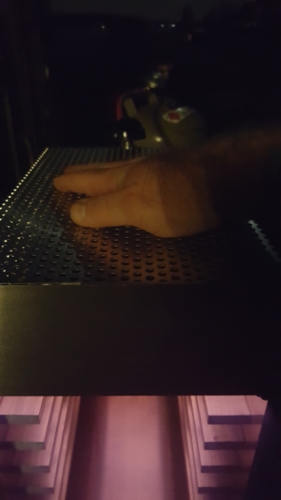 |
50. Mich hat es sehr überrascht, dass man im laufenden Betrieb die Hand oben auf den OHG legen kann ohne Brandblasen zu bekommen. Ein paar cm tiefer ist der Grill auf ca. 900°C angeheizt. Wie ich in der Zwischenzeit erfahren habe wird der OHG im Dauerbetrieb doch auch oben recht warm. Also FINGER WEG :-) |
| 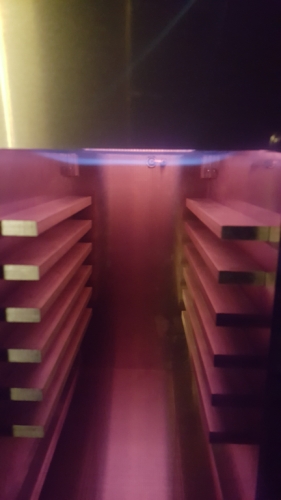 |
51. Der direkt Blick von vorne. Das Plasma erzeugt wie bereits beschrieben auf der oberseten Stufe ca. 900°C. Je tiefer man das Grillrost einschiebt desto "kühler" wird der Grill. Auf der untersten Stufe herrschen noch ca. 150°C. |
| 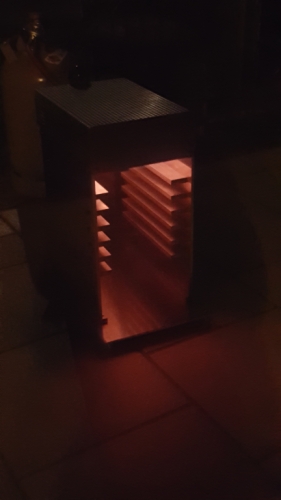 |
52. Wer kein Fleisch griffbereit hat kann den OHG auch als Rotlichtbeleuchtung benutzen :-) |
| 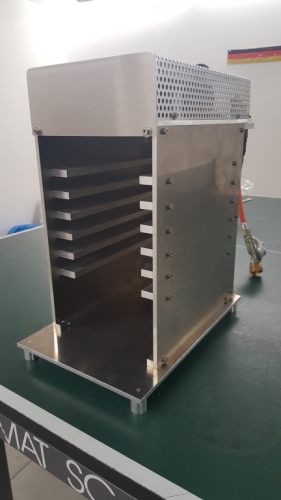 |
53. Der OHG nach dem Testlauf. Keine Verfärbungen, keine Verzüge. Test bestanden! |
| 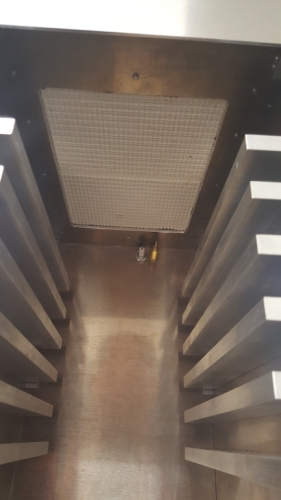 |
54. Die Brennerkeramik ist ebenfalls wie neu :-) |
| 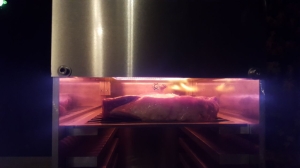 |
55. Hier noch ein paar Bilder vom reellen Einsatz... |
| 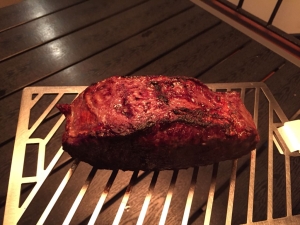 |
56. Nach ca. 45...60 Sekunden ist die Fleischoberseite fertig. |
| 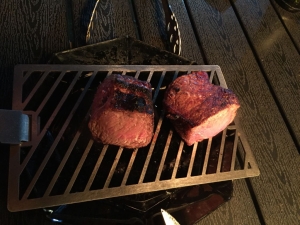 |
57. Guten Hunger :-) |
|
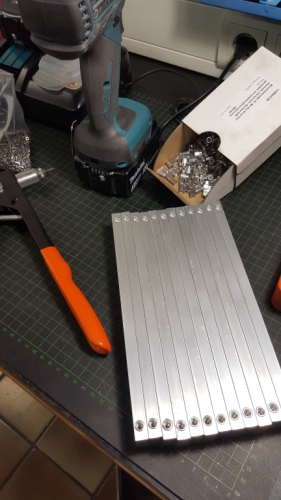 |
58. Nachdem sich die ersten 4 OHGs in der Praxis sehr gut bewährt haben durfte ich noch weitere 10 herstellen. Ich habe alle Zeichnungsanpassungen von der Version 1.0 auf den aktuellen Stand
2.0 gebracht und das Material bestellt. Da ich keine Lust hatte 240 Gewinde in die Führungsschienen zu schneiden habe ich einmal Aluminium Einzugmuttern getestet. Ich bin schwer davon beeindruckt wie einfach sich die Nietmuttern verarbeiten lassen und welche Kräfte die Muttern aushalten. |
| 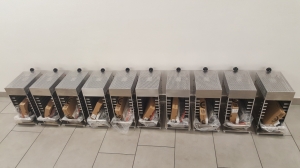 |
59. Da ich viele Teile im Sandwich bohren konnte waren alle OHGs innerhalb von 2 Wochen fertig gestellt. (Ich habe leider nicht die Zeit kontinuierlich an meinen Projekten zu arbeiten.) Naja, 10 Stück in einer Reihe sehen auch ganz gut aus :-) |
| 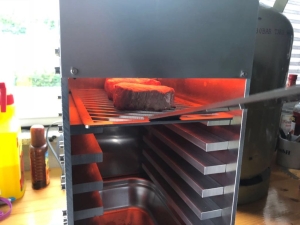 |
60. Ein sehr netter Bekannter hat seinen OHG heute Morgen abgeholt und mir ein paar Stunden später ein paar Bilder geschickt :-) |
| 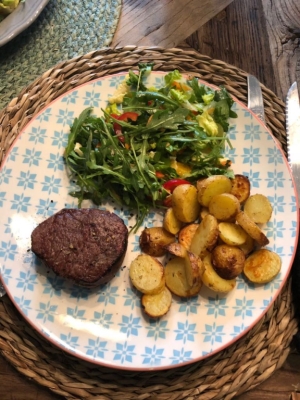 |
61. Danke Martin |