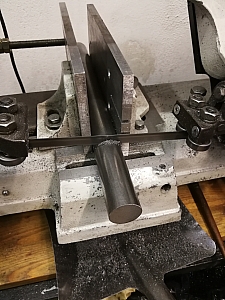 |
Wie auch schon im letzten Jahr möchte ich hier viele kleine Projekte zusammen vorstellen. Für diese Miniprojekte lohnt es sich nicht immer wieder neue Seiten auf der Homepage zu erstellen. Ein sehr netter Bekannter benötigte für 4 Steinbrechermodelle die Hauptexcenterwellen für das Brechermodul. Da an diesen Wellen auf beiden Seiten ein Schwungrad angebracht werden sollte mussten die Wellen so hergestellt werden, dass die beiden Wellenenden exakt zueinander symetische laufen. Hier wird gerade das Rohmaterial für die Spannhülse abgelängt. |
 |
Mit dem CAD System wurde ermittelt wie weit der Excenter aus der Mitte liegen muss. |
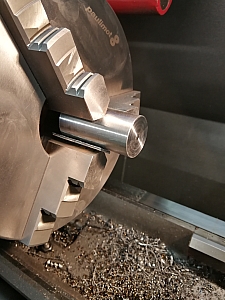 |
Die Spannhülse wurde im ersten Versuch mit entsprechenden Unterlagen versehen. Leider funktionierte dies nicht sehr gut und ich habe später die Hülse mit einem Vierbackenfutter noch einmal hergestellt. |
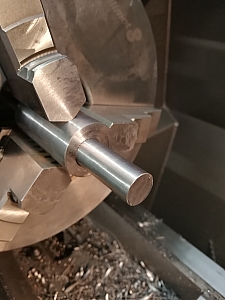 |
Hier wurde bereits die aussermittige Bohrung für die Wellenaufnahme eingebracht. |
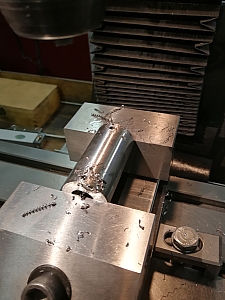 |
Die beiden Madenschrauben verhindern ein Verdrehen der Welle.... |
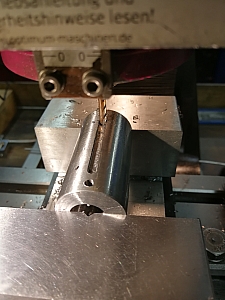 |
... und der eingefräste Schlitz sorgt für den richtigen Halt beim Drehen der Excenter. |
 |
So sitzt die Spannhülse auf der Welle.... |
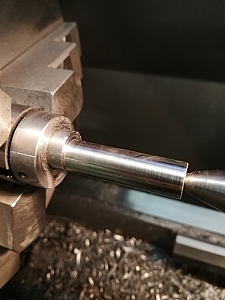 |
... und hält die Welle bei der Bearbeitung bombenfest. |
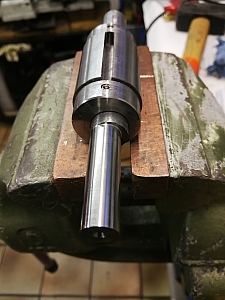 |
Dadurch, dass die Hülse auf der Excenterwelle verschraubt ist können beide Wellenenden bearbeitet werden ohne die Welle zu verdrehen. Hier ist die erste Excenterwelle fertig bearbeitet. |
 |
Ein sehr netter Modellbaukollege benötigte für das Funktionsmodell eines Steinbrechers ein paar Kettenräder. Diese mussten am Bund abgedreht werden. Da sich die Zahnräder extrem schlecht in einem normalen Backen- oder Spannzangenfutter spannen lassen habe ich mir eine spezielle Spannvorrichtung angefertigt. Hier wird gerade die spätere Zentrierbohrung in das Basisteil der Spannvorrichtung eingebracht. |
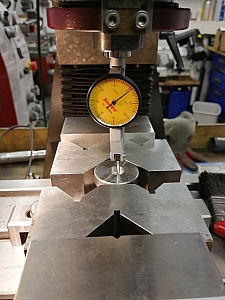 |
Nachdem das Basisteil abgestochen wurde konnte dieses Bauteil auf der Fräse ausgerichtet ... |
 |
... und die drei Befestigungsgewinde eingebracht werden. |
 |
Die drei Gewinde M3 x 0,75 wurden geschnitten. |
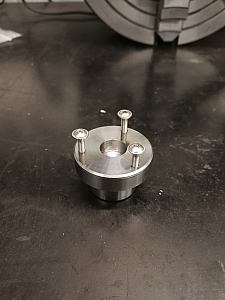 |
Das Basisteil ist fertig.... |
 |
.... und sollte funktionieren. So sitzt später das Zahnrad in der Aufspannung. |
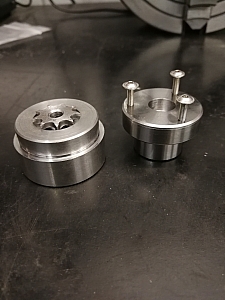 |
Die Anfertigung des passenden Deckels habe ich nich weiter bebildert. |
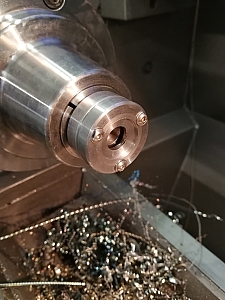 |
Hier sind beide Teils der Spannvorrichtung in ein Spannzangebfutter eingespannt. |
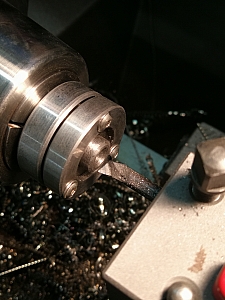 |
Un schon konnte der Bund des ersten Zahnrades abgedreht werden.... |
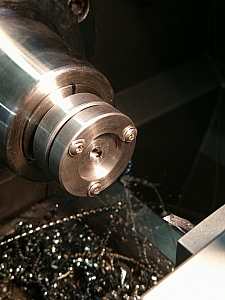 |
... dabei wurde auch direkt die Spannvorrichtung auf das entsprechende Maß mit eingekürzt. |
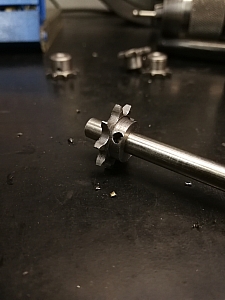 |
Passt perfekt .... also konnten die restlichen Zahnräder ebenso eingekürzt werden. Die Wiederholgenauigkeit der Spannvorrichtung hat mich wirklich erstaunt. 1/100mm ist damit machbar. |
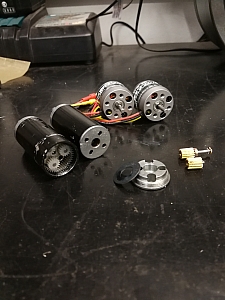 |
Auch hierbei handelt es sich um einen Umbau für ein Funktionsmodell eines Steinbrechers. Die Planetengetriebe eines DC Antriebes sollten auf Brushless-Motoren umgerüstet werden. |
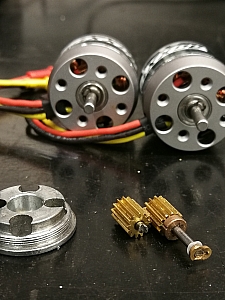 |
Dabei wurden von den alten DC Motoren die Antriebsritzel mit einer Trennscheibe demontiert .... |
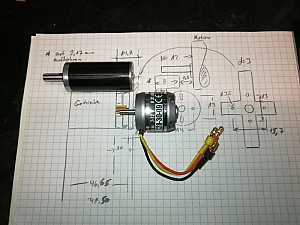 |
... und alle wichtigen Verrechnungsmaße in einer Skizze festgehalten. Der spätere Sitz des Ritzels auf der Welle des Bruschless-Motors ist sehr wichtig für die Lebensdauer des Getriebes. Weiterhin wurde die Befestigung der Motor-Getriebeeinheit geplant und mit in die Konstruktion eingebracht. ...Es muss nicht immer 3D-CAD sein :-). |
 |
Nachdem ich die Ritzel mit Wärme behandelt hatte konnten die Wellenenden ausgetrieben werden. Sorry, der Nagel passte besser als mein kleinster Austreibdorn. |
 |
Schritt Nummer eins ist geschafft.... |
 |
.... und nun konnten die Aufnahmebohrungen angepasst werden. |
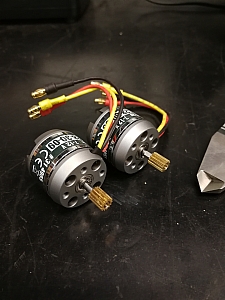 |
Passt alles wie gewollt. |
 |
Anschließend habe ich angefangen die Adapterplatte für die Getriebe-Motor Befestigung herzustellen. Das Basismaterial ist ein Rundmaterial 42CrMo4. Hier wird gerade die Zentrierung für die spätere Durchgangsbohrung eingebracht. |
 |
Nachdem die Bohrung hergestellt war konnten die benötigten Scheiben abgestochen werden. |
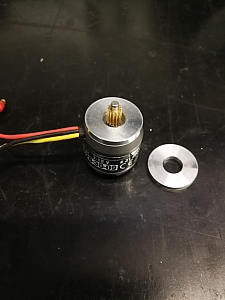 |
Sieht alles soweit gut aus .... |
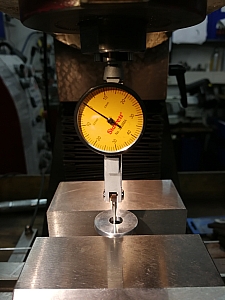 |
... und nach dem Zentrieren auf der Fräse .... |
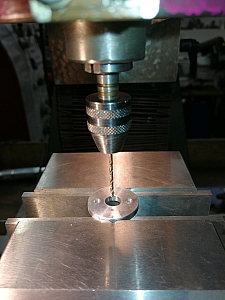 |
.... wurden die Befestigungslöcher für das Motoren- und Getriebegehäuse eingebracht. |
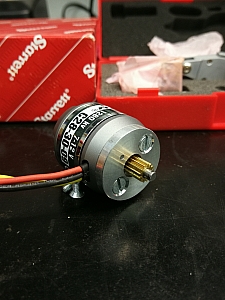 |
Die Motorenseite passt ..... |
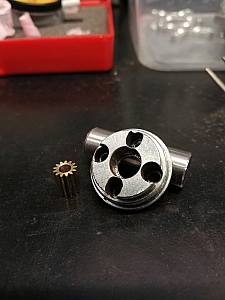 |
.... und die Getriebeseite ebenfalls. |
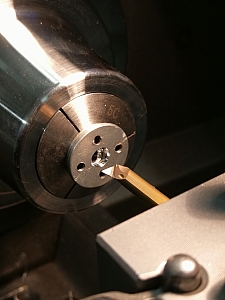 |
Nun wurde noch ein Absatz eingebracht .... |
 |
... und die erste Probemontage sah sehr gut aus. Leider würde der kleine Motor so sehr schnell den Hitzetot sterben da alle Belüftungslöcher durch die neue Montageplatte verdeckt wurden. |
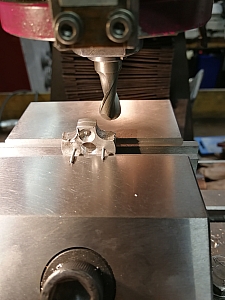 |
Also wurde hier etwas brutal nachgeholfen.... |
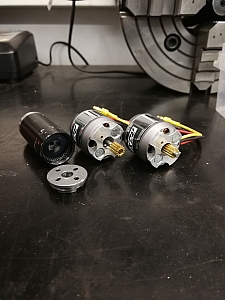 |
... und für genug Luft gesorgt. |
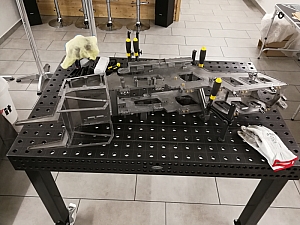 |
... und schon wieder etwas für ein Funktionsmodell eines Steinbrechers :-) Hier kann man den Basisrahmen des Modells auf meinem Schweißtisch (1200mm lang) sehen. Es wurden ein paar Schweißnähte verstärkt .... |
 |
... da mein Freund Bedenken hatte, dass die kleinen Nähte (Micro-WIG) evtl. bei der Belastung durch den Brecher reißen könnten. |
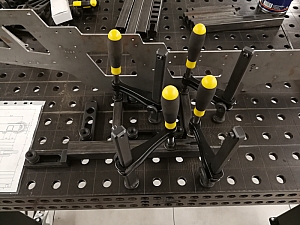 |
Zusätzlich wurde der Basisrahmen für den Kettenantrieb benötigt. Die gelaserten Rohre wurden exakt an den Seitenwänden des Modells ausgerichtet, auf dem Schweißtisch verspannt und mit dem WIG Gerät verbunden. |
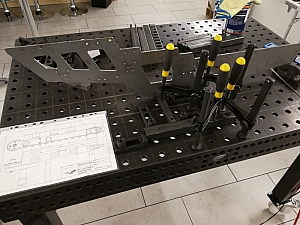 |
Alles passte exakt und ich habe nach dem Schweißen lange gewartet damit alles abkühlt. Somit sollte der Verzug des Rahmens auf ein Minimum reduziert werden. |
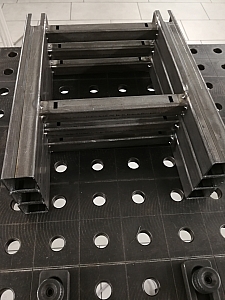 |
Hier sieht man, dass mehrere Modell parallel gebaut werden und die Rahmen von mir an allen erdenklichen Stellen vorab geheftet wurden. Leider haben sich die Rahmen dann doch teilweise so stark verzogen, dass ich damit nicht zufrieden war. Eine Montage war zwar sauber möglich, ich wollte das aber so nicht abgeben..... |
 |
... die Feinmechanikerlösung ist eine 20t hydropneumatische Presse, die seit ein paar Wochen in meiner Werkstatt steht. |
 |
Der Rahmen wurde an 3 Stellen unterlegt und auf eine massive Stahlplatte gespannt. Die hochstehende Seite wurde von oben hydraulisch belastet und so der Verzug aus dem Rahmen gedrückt. |
 |
Das Ergebnis hat mich überzeugt und somit sind die Teile fertig für den späteren Einbau. Der Verzug liegt nun sehr deutlich unter 1mm. |
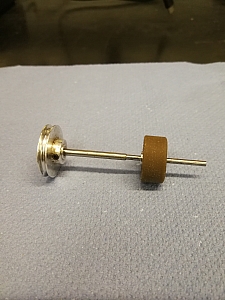 |
Ein Arbeitskollege eines sehr netten Bekannen benötigte für ein Auswuchtgerät für Modellbaureifen eine neue Auswuchtwelle. |
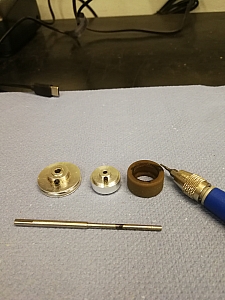 |
Die Herausvorderung war hier die extreme Länge im Verhältnis zum Durchmesser und die sehr genauen Abmessungen. Der Antriebsflansch und Reifenhalter ließen sich leicht demontiren.... |
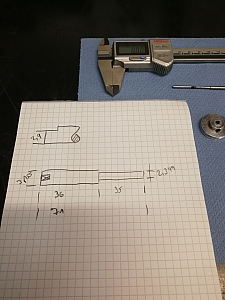 |
... und so konnte die Welle vermessen werden. Selbstverständlich habe ich parallel zum Meßschieber auch eine Meßuhr verwednet. |
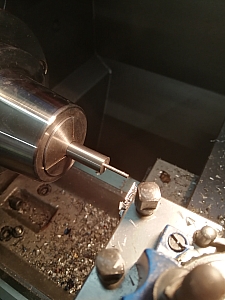 |
Wie man in den einschlägigen Youtube-Videos immer wieder sehen kann sollte man sehr dünnen und lange Bauteile in einer Zustellung drehen um die Verbiegung bei der spanenden Bearbeitung gering zu halten. Das habe ich hier ebenfalls so gemacht. |
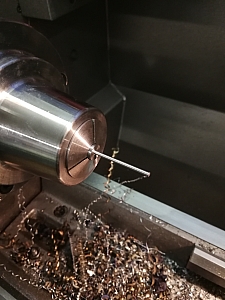 |
Der dünnste Durchmesser ist fertig bearbeitet und von vorne bis hinten exakt gleich. |
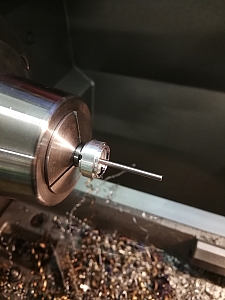 |
Die Montagefelge für den Reifen geht saugend auf die Welle. |
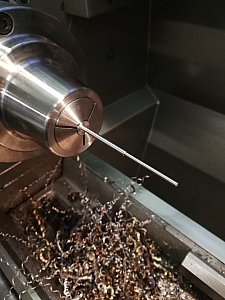 |
Da mein Spannzangenfutter sehr genau arbeitet konnte ich die Welle ausspannen und weiter aus dem Futter heraus ziehen um den nächsten Durchmesser zu bearbeiten. Hierbei war der Rundlauffehler mit einer 1/100mm Meßuhr nicht anmessbar. |
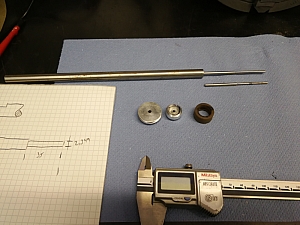 |
Das Original und der Nachbau (noch am Stück)... |
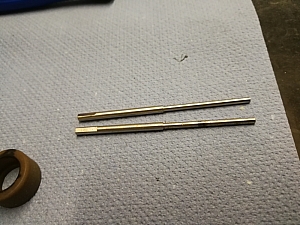 |
.... und hier bereits mit einer kleinen Abflachung für die Schraubfixierung versehen. Diese habe ich mit der Stichelschleifmaschine angeschliffen. |
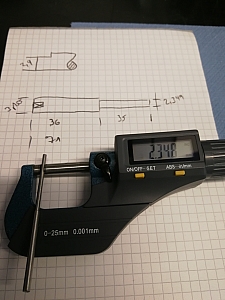 |
2.349mm war das Sollmaß....2.348mm wurde erreicht..... |
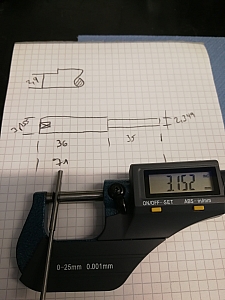 |
.... 3.155mm zu 3.152mm sind für mich ebenfalls ok. Da ich in meinem Bastelkeller keine konstante Temperatur habe kann ich die 1/1000mm selbstverständlich nicht reproduzieren. Ich habe aber beide Wellen direkt hintereinander verlessen und die Abweichungen waren wirklich so gering. |
 |
Wieder ein Bauteil fertig..... |
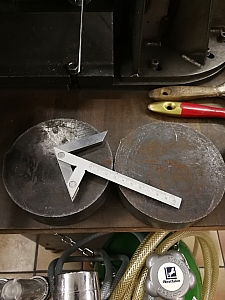 |
Ebenfalls für den Prototypen eines Steinbrechermodells wurden die Schwungräder für den Antrieb der Brechereinhet benötigt. Das Ausgangsmaterial besteht aus plasmageschnittenen Stahlronden. Ich vermute, dass es sich um S235JR handel. |
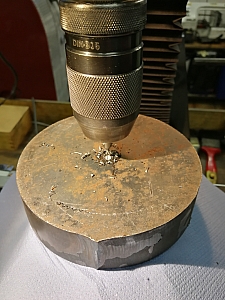 |
Zuerst wurde die Mitte der Ronden grob fixiert und eine Zentrierbohrung gesetzt. Auf dem Bild kann man sehen, dass eine exakte Mittenbestimmung nur schwer möglich war. |
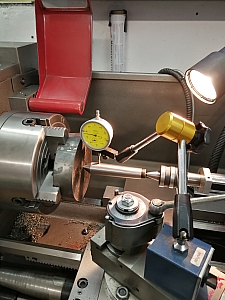 |
Im Vierbackenfutter konnten die Ronden aber sicher gespannt und ausgerichtet werden. |
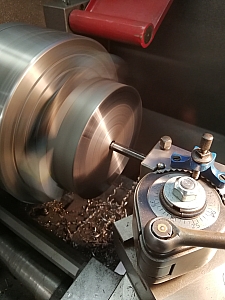 |
Nach dem Plandrehen durde eine Zentrierbohrung eingebracht.... |
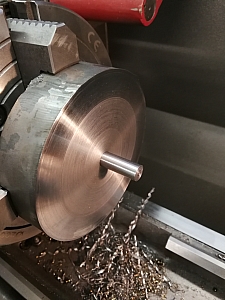 |
... die exakt zum späteren Durchmesser der Antriebwelle passt. |
 |
Nun wurde eine Spannvorrichtung hergestellt und mit einem Innengewinde und einem Zentrierbund versehen. |
 |
Die Stahlronden konnten somit sehr gut gespannt und mit einer mitlaufenden Körnerspitze unterstützt werden. |
 |
Der Außendurchmesser der Ronde war schnell bearbeitet .... |
 |
... und auch die Oberflächengüte war für mich in Ordnung. |
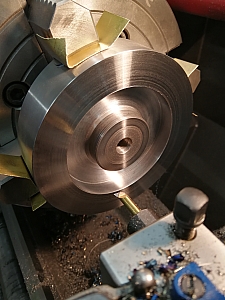 |
Nach Zeichnung sollten die Schwungräder einen innenren Absatz bekommen um Gewicht zu sparen. |
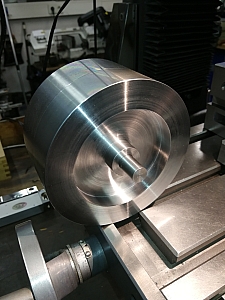 |
Hier sind bereits beide Schwungräder fertig bearbeitet und auf eine Welle aufgeschoben. Es passt alles perfekt. Das Gewicht ist für eine Modellbauanwendung schon stattlich. |
 |
Damit beim Antrieb auch alles funktioniert sollten die Schwungräder noch mit 3mm Keilnuten ausgestattet werden. |
 |
Vielen Dank an Jürgen der mich immer bei diesen Arbeiten in seine Werkastt lässt :-). |
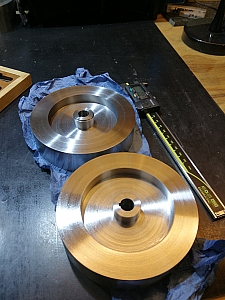 |
Die einsatzbereiten Schwungräder |
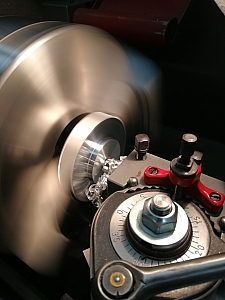 |
Ebenfalls zum Antrieb der Steinbrechermodelle gehören verschiedene Zahnriemenscheiben. Hier wird gerade der Innendurchmesser eines Zahnriemenrades an den Wellendurchmesser des Antriebes angepasst. |
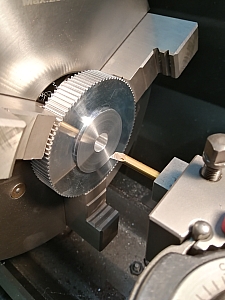 |
Für diese Arbeiten benutze ich am Liebsten die kleinen Drehmeißel der Firma Horn. |
 |
Das antriebsseitige Zahnriemenrad passte perfekt in eine Spannzange und konnte somit sehr einfach .... |
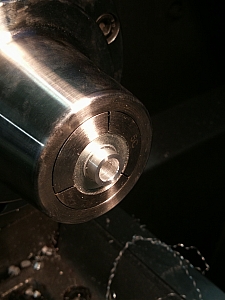 |
... bearbeitet werden. |
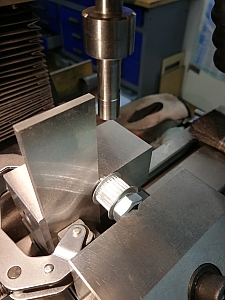 |
Hier wurde ein Parallelanschlag benutzt um den Bund des Zahnriemenrades mit dem Kantentaster anmessen zu können. |
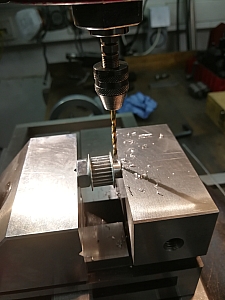 |
Anschließend konnte das Loch für die spätere Fixierung mittig in den Bund eingebracht werden. |
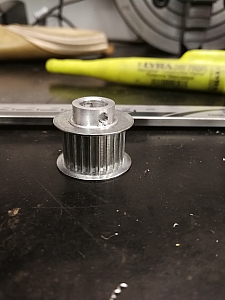 |
Das fertige Antriebsrad.... |
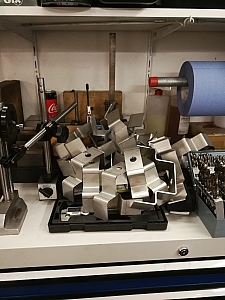 |
Ein sehr netter Bekannter benötigte für eine neue Poolumrandung und -entwässerung ein paar zusammengeschweißte Bauteile aus Edelstahl. Die Einzelteile kamen bei mir schon gelasert und perfekt gekantet an..... |
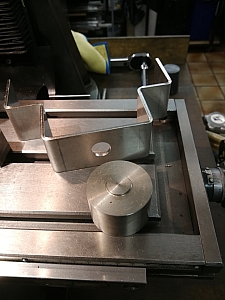 |
Aus diesen Teilen wurden Stützen für ein Entwässerungssystem geschweißt. |
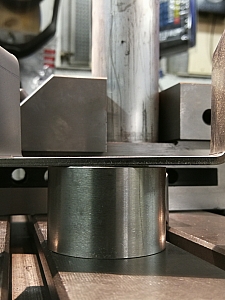 |
Beim Zusammenstecken zeigte sich aber, dass das Laserschneiden so genau war, dass der Drehradius der Zentrierung den sauberen Zusammenbau verhinderte. |
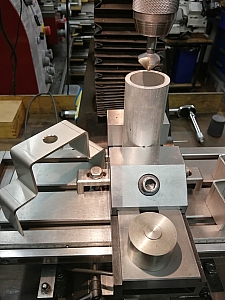 |
Also habe ich ein Rohrendstück eingespannt .... |
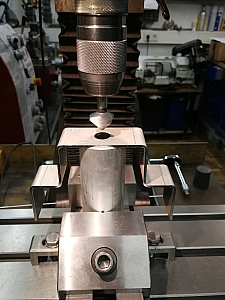 |
... und als Auflage beim Senken benutzt. |
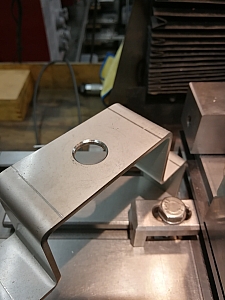 |
Die Senkung ist gerade so groß, .... |
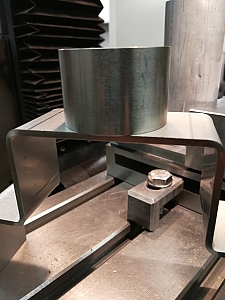 |
... dass ein Zusammenstecken sauber möglich war. Nun liegt das Blech vollflächig auf. |
 |
Nachdem alle Teile gesenkt und mit Aceton gereiningt wurden .... |
 |
... konnten die Schweißpunkte mit dem WIG Schweißgerät gesetzt werden. |
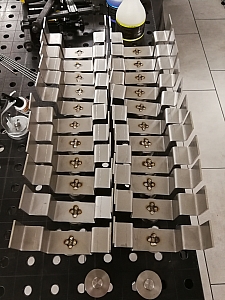 |
Ein paar Minuten später waren die Halter fertig verschweißt. |
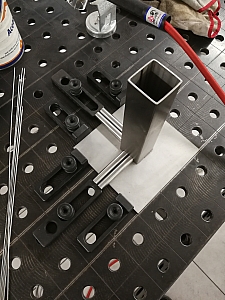 |
Nun ging es an ein paar Stützen für den Unterbau der Poolumrandung. Diese Teile waren ebenfalls perfekt vorbereitet und mussten nur noch verschweißt werden. Damit ich nicht immer wieder alles ausmessen musste habe ich mir ein paar Anschläge am Schweißtisch ausgerichtet.Damit ist die Kleinserie ein Kinderspiel.... |
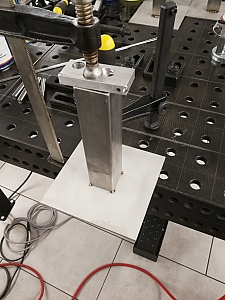 |
Die Heftpunkte wurden mit Hilfe der Anschläge gesetzt und anschließend wurden die Vierkantrohre mit den Platten verschweißt. |
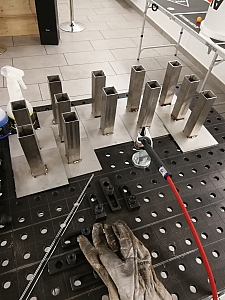 |
Diese Arbeit war ebenfalls in ein paar Minuten erledigt. Von den weiteren Unterbauteilen habe ich leider die Bilder gelöscht. Die Teile sahen aber ähnlich aus und die Abreiten waren fast identisch. |
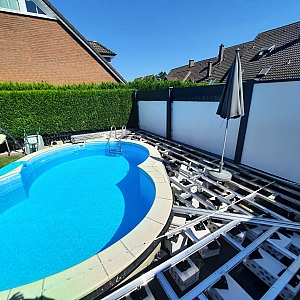 |
Mein Bekannter hat mir ein paar Bilder der fertigen Unterkonstruktion gesendet. Hier wurden die Bauteile an Ort und Stelle fixiert. |
 |
Sieht alles sehr stabil aus .... |
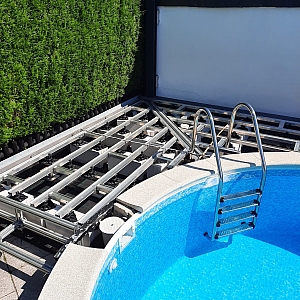 |
... und sollte die begehbare Poolumrandung .... |
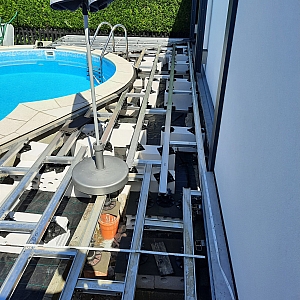 |
... auf jeden Fall tragen. Zusätzlich gibt es eine interne Entwässerung die Pool- und Regenwasser sicher ableitet. |